New 3D printing processes and materials even for complex geometries
- Gastautor
- 5 days ago
- 5 min read
How a medium-sized company benefited from the expertise of an external design office.
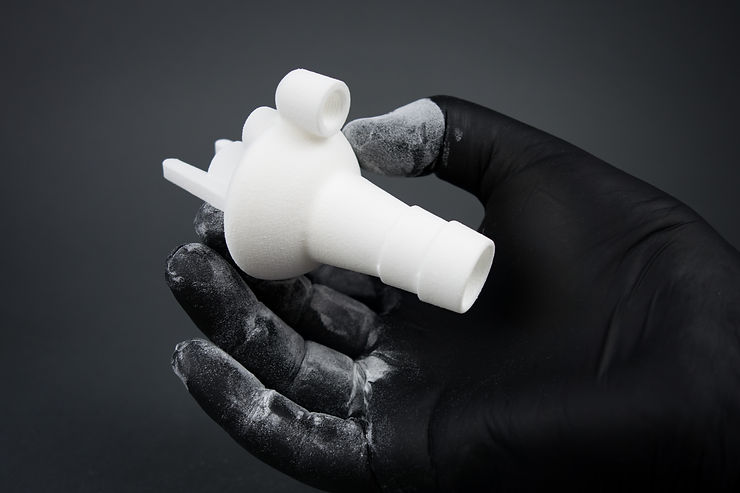

Süß & friends, founded by mechanical engineer Philipp Süß, is one of the companies represented in the Digital Ruhr region. It offers medium-sized businesses access to digital manufacturing processes. One of its customers manufactures special machines for the packaging industry and was looking for a new funding option for the adhesives used in production. The solution is based on new additive manufacturing methods – thus offering a cross-industry perspective on the new opportunities created by digitalization.
background
Baumer hhs GmbH is a global manufacturer of adhesive application and quality control systems. Baumer hhs products are used in applications such as pharmaceutical packaging, envelopes, and shipping cartons. The company is considered highly innovative, expanding its technological leadership through the continuous development of new solutions. The adhesive for the melters is in the form of pea-sized granules. The granules are conveyed by a complex system comprising several mechanical and electrical components.
"The engineers at Baumer hhs had developed an innovative, new concept for conveying the adhesive granules," reports Marco Abelius, Design Project Manager at Baumer hhs. "All functions, such as suction, vibration, and conveying, were to be performed by a single component." This concept, called the "suction conveying nozzle," envisaged that operation would be made possible solely by air pressure. A power connection was also deliberately omitted. "However, the problem," says Abelius, "was that the suction conveying nozzle, due to its complex geometry,
internal channels could not be produced using conventional methods.”

Initial attempts with industrial 3D printing* also failed. Although this new process group can produce virtually any imaginable geometry, it also presents its own unique challenges. Unwanted residual powder remained in the internal channels, and costs fluctuated greatly depending on the process and material.
Industrial 3D printing
Industrial 3D printing is a collective term for the application of various 3D printing technologies in industrial applications. This involves the fully automated construction of a component from a powdered, liquid, or wire-like starting material. A computer-generated, high-quality 3D model of the component serves as the basis. Industrial 3D printing differs significantly from the 3D printer found in a hardware store. Professional
Machines are based on completely different physical principles and can easily cost a quarter of a million euros. The term "additive manufacturing" has therefore become the accepted technical term.
Today, hundreds of different processes with diverse properties and materials are available on the market. These materials range from steel, aluminum, and titanium to plastics, ceramics, and concrete, as well as many other useful materials. In order to make a suitable selection and implement a sensible, promising application, both highly specific technical expertise and a comprehensive market overview are absolutely essential.
Task
The task for Süß & friends was to technically develop the suction nozzle and then create it as a standard item for prompt reordering in small batches. "First, however, as is often the case with 3D printing processes, it was necessary to select not only the most suitable manufacturing process, but also the most suitable material," recalls Philipp Süß, Managing Director of Süß & friends. Only in the next step did the mechanical engineer adapt the design and create the production data, taking into account the required quality specifications.
"Creating a product as a standard item represents the ultimately standardized process through the entire value chain, because 3D printing is normally only one part of this chain. The necessary downstream processes are typical in the manufacture of technical products," explains Süß. These include, for example, post-processing, a wide variety of finishing methods, and quality control. Packaging and shipping also often play a role. Süß & friends can cover this entire value chain. "In addition to our technical expertise, our customers appreciate that our design office provides them with a single point of contact for all tasks that arise," says the managing director.
challenges
The complex geometry of the suction nozzle was impossible to manufacture conventionally due to its internal channels. Furthermore, industrial 3D printing initially left unwanted powder residue in the internal channels. The selected material also had to be able to withstand high levels of wear. Furthermore, it was important to integrate connection threads for compressed air valves. Finally, due to the enormous cost pressure, production had to be cost-effective even for small batch sizes – no easy task, as the costs of additive manufacturing vary greatly depending on the process and material.
Solution
To solve these problems, Süß & friends developed a multi-step manufacturing process consisting of digital production, residual powder removal, and surface finishing. To do this, the design was first adapted. As a basis for digital production, a digital 3D product model containing all the necessary information and geometries was created from the design data.
The nozzle's base body is now manufactured fully automatically by laser from a special powdered plastic. "During this manufacturing process, the final geometry is created, including all connection threads, channels, and functional surfaces," explains Süß. "But unfortunately, unwanted powder residues still remain in the internal channels."

To remove these, Süß & friends has developed a new procedure that draws on methods and tools from medical technology. The basic idea stems from a concept that Süß developed years ago at the University of Duisburg-Essen.
Ultimately, the goal is to further improve wear resistance. To achieve this, Süß refines the surface with a high-strength special plastic.
The functionality of the resulting component has been confirmed through endurance tests. As a result, the suction conveyor nozzle is now an integral part of a Baumer hhs product.
Customer benefit
Project manager Marco Abelius doesn’t need to think long to describe the customer benefits:
"With the 'suction nozzle' component, we replace several expensive mechanical and electrical components. This not only saves storage costs but also eliminates potential sources of error from the process. Furthermore, the suction nozzle can be economically reproduced by Süß & friends within a few days and in small quantities. We are very satisfied with the collaboration and the result."
Marco Abelius
Project Manager
Baumer hhs GmbH


Contact Süß & friends Baumer hhs GmbH Philipp Süß Mrs Petra Schneiders Augustastraße 66 Adolf-Dembach-Straße 19 45476 Mülheim adR 47829 Krefeld phone 0208 3760 733 0 phone +49 2151 4402-105 fax +49 2151 4402-111 E-Mail hello@suess-friends.com E-Mail pschneiders@baumerhhs.com Web www.suess-friends.com Web www.baumerhhs.com
This article by Michael Houben, owner of Metamorphose ( Link ) , originally appeared in Digitales Pott.
Comments